Navigating the labyrinth of construction tools can be overwhelming, especially when performance is paramount. If you've found yourself staring down aisles of concrete grinding wheels, pondering which one to choose, worry not
This detailed guide is here to walk you through the selection process step by step. Whether you're a seasoned professional or a DIY enthusiast, understanding the nuances of different grinding wheels can directly impact the efficiency and outcome of your projects.
Why the Right Wheel Matters
Before we plunge into the specifics, it's crucial to understand why selecting the right concrete grinding wheel is not just about preference, but necessity. The concrete surface's composition, hardness, and the type of grinder all necessitate different grinding wheel characteristics for optimal effectiveness. A misconception here can result in wasted time, inefficiencies, or even a subpar finish.
In the world of concrete grinding, precision is often synonymous with time and money. Whether you're smoothing out a garage floor or polishing an industrial surface, your tools are your armory. The concrete grinding wheel is one of the most critical tools in your inventory, acting as the final arbiter between an average job and a masterpiece.
Types of Concrete Grinding Wheels
Diamond Grinding Wheels
Diamond grinding wheels are the gold standard for any heavy-use concrete or stone project. Designed with industrial-grade diamonds bonded to the wheel’s substrate, diamond wheels are incredibly durable and provide a superior finish.
They are the go-to choice for grinding concrete with utmost precision, irrespective of the intricacies of the job. The diamond abrasive on the wheel's surface can grind down thick concrete layers and imperfections smoothly and efficiently.
Silicon Carbide Grinding Wheels
When it comes to jobs requiring less intense precision, silicon carbide wheels present themselves as a cost-effective alternative. This type of wheel is suitable for soft concrete surfaces or when working with coatings, paints, or adhesives. Though they are less tough than diamond wheels, they can offer a finer finish in general-purpose applications.
Aluminum Oxide Grinding Wheels
Aluminum oxide wheels are often used for grinding most nonferrous metals and woodworking, but they can also play a role in certain concrete-grinding applications. They're known for their versatility and longer lifespan compared to silicon carbide wheels. If you're working with cement residues or a concrete surface that isn’t too abrasive, this could be a suitable choice.
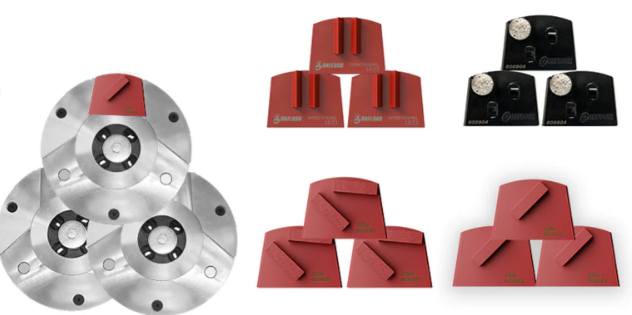
Factors to Consider When Choosing
Selecting the right type of concrete grinding wheel is more than just choosing between diamonds or other materials. Several factors must be addressed to ensure the wheel's compatibility with the surface and the longevity of the grinding process.
Grit Size
Because it directly affects the smoothness of the finished surface and the speed at which material is removed, grit size is an important consideration. In the realm of concrete grinding, fine grit is specified by a higher grit number, which translates to a smoother finish and slower material removal. However, when heavy grinding or material removal is needed, a coarser grit is ideal with lower grit numbers.
Wheel Hardness
Grinding wheel hardness is vital to maintain a balance between abrasion and wear resistance. A softer wheel will wear down faster, which can be advantageous for projects requiring finer finishes. Conversely, harder wheels can remove more material but may produce a rougher result.
Wheel Bond
“Bond” refers to how the abrasive material is held in the wheel. Different bonds provide varying hardness and help control the characteristics of the wheel. For instance, a vitrified bond can be ideal for precision grinding, while a resin bond can offer a versatile mix of performance for general applications.
Wheel Shape
The shape of the wheel also plays a significant role in the grinding process. Flaring cup wheels, straight cup wheels, and wheel edges have specialized uses and are matched to specific grinding requirements.
Applications and Best Practices
When you've honed in on the most suitable grinding wheel for your project, it's time to focus on the application and best practices to maximize its potential.
Matching the Wheel to the Task
Each concrete grinding wheel type is better suited to different tasks. Diamond wheels excel at heavy grinding and preparing rough surfaces for coatings, while silicon carbide wheels can be more delicate when polishing or removing softer materials. Make sure your chosen wheel aligns with the project's requirements.
Safety Precautions
Concrete grinding can be hazardous if not conducted with the proper safety measures. Silica dust extraction systems, protective equipment, and secure fastening of the wheel are non-negotiable components of any worthwhile concrete grinding venture.
Maintenance Tips
Once the job is underway, it's important to keep in mind the wheel's condition and take preventative steps to ensure its longevity. Dressing the wheel periodically, cleaning it after use, and keeping track of any damage are all key maintenance practices.
ADVANCED TOOLS FOR CONCRETE GRINDING
One innovation that is revolutionizing the grinding industry is the advent of quick-change tooling, which allows for rapid switching between different grinding wheels.
Onfloor is a pioneer that has patented this technology, offering a suite of on-the-fly exchangeable grinding attachments that are a godsend for professionals requiring maximum efficiency without compromising on quality.
From the diamond grinding pads to hook and loop sandpaper, these quick-change tools maximize the potential of your grinder and minimize downtime.
FAQs
Q: What is quick-change tooling?
A: Onfloor's patented quick-change tooling is a technology used to rapidly switch between different grinding wheels or attachments. This innovation allows for improved efficiency and flexibility during wet or dry concrete grinding.
Q: Why Onfloor?
A: Onfloor's versatile and durable quick-change tools, combined with their high-performance grinding machines, make them a top choice for professionals in the concrete grinding industry. Their commitment to innovation and customer satisfaction makes them a leader in the field.
Q: Is concrete grinding only used for preparing surfaces?
A: No, concrete grinding can also be used for marble polishing and removing softer materials such as epoxy coatings. It is a versatile technique that can be adapted to various applications.
For prepping floors, we recommend you choose the OF30Pro Multi-Surface Floor Grinder, which is ideal for removing coatings and preparing surfaces with its versatile Quick-Change tooling system. For polishing and finishing, the OF16S-H Floor Grinder offers superior performance and control.
Q: Can I use a concrete grinding wheel on other materials besides concrete?
A: We don’t recommend using a concrete grinding wheel on other materials, as it is specifically designed for use on concrete surfaces. However, the OF16S-H Floor Grinder can also be used on terrazzo patio, granite, and stone surfaces. For wood surfaces, the OF20Pro Multi-Surface Floor Grinder offers a specialized wood grinding attachment.
Q: Can I use one type of wheel for all my concrete grinding needs?
A: No, it's important to match the wheel type to the specific task at hand for optimal results. Using the wrong type of wheel can result in scratches, a subpar finish, or damage to the surface being worked on.
Q: What is the best way to maintain my concrete grinding wheels?
A: Regularly dressing and cleaning the wheels, as well as monitoring for any damage, are crucial maintenance practices to ensure your wheels last longer and perform at their best.
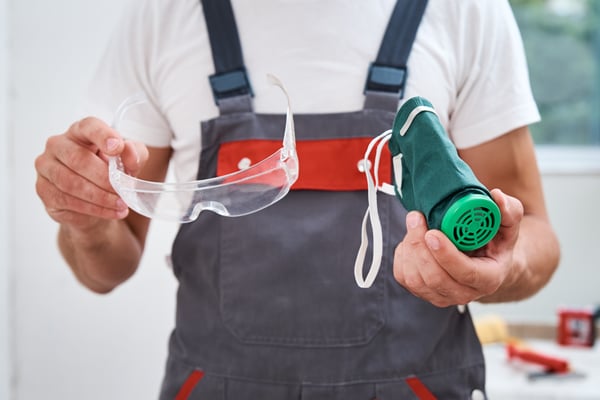
Q: Are there any safety precautions I should take when using concrete grinding wheels?
A: Yes, it is important to properly secure the wheel, use dust extraction and filter systems, and wear the necessary protective equipment to ensure safety during the grinding process.
Q: What is the difference between a vitrified bond and a resin bond for grinding wheels?
A: In the world of bond materials, vitrified bonds provide a more rigid and durable bond, making them suitable for precision grinding. Resin bonds offer a versatile mix of performance and are often used in general grinding applications.
Q: Can I use different types of grinding wheels on the same project?
A: Yes, it is common to use multiple types of grinding wheels for different stages or areas of a project. This allows for optimal results and efficiency. Onfloor's quick-change tooling makes this process even easier.
Q: How do I know which grit number to use for my project?
A: The grit number refers to the coarseness of the wheel and its ability to remove material. A lower grit number is more aggressive, while a higher number will produce a finer finish. Consider the type of material and desired result when selecting the appropriate diameter and grit number for your project.
Conclusion
Selecting the right concrete grinding wheel is an art as much as it is a science. It involves an intricate balance of understanding the wheel's composition, the material to be ground, and the environmental and safety factors involved. However, with the wealth of information available and the advancements in tooling technology, making the right choice doesn’t have to be a shot in the dark.
A single wheel can transform a challenging grind into a seamless process, accentuating the professional's skill and dedication to their craft. This guide serves as a compass, ensuring that as you venture forth into the world of concrete grinding, you do so with the confidence of a well-informed craftsman, ready to create and conquer with every revolution of the wheel.
After all, it's often the unsung heroes in our masonry toolkits that make the loudest statements in our projects' eminence.
2 comments